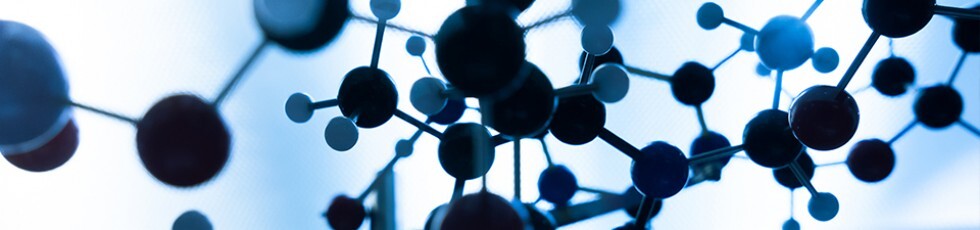
Grundlagen der Produktsysteme
Die chemische Metallabscheidung gewährleistet eine sehr konstante und gleichmäßige Schichtdickenverteilung auch bei Bauteilen mit komplexer Geometrie.
- Chem. Nickel als Basis
- DIAprotect GRUNDLAGEN
- DIAGRIP GRUNDLAGEN
- DIAGlide GRUNDLAGEN
- DIAPROTECT GRUNDLAGEN
- DIASHIELD GRUNDLAGEN
Im Gegensatz zur elektrolytischen Abscheidung geschieht die Chemisch Nickel – Beschichtung ohne äußere Stromquelle; d.h. auf rein chemischem Wege.
Daraus resultieren die besonderen Eigenschaften dieser Schichten:
Die chemische Metallabscheidung gewährleistet eine sehr konstante und gleichmäßige Schichtdickenverteilung auch bei Bauteilen komplexer Geometrie.
Auch Innengeometrien, Bohrungen und Hinterschneidungen werden absolut gleichmäßig beschichtet.
Zur Abscheidung der Chemisch Nickel – Schichten wird ein Reduktionsmittel benötigt. In den meisten Fällen handelt es sich dabei um eine phosphorhaltige Verbindung. Verfahrensbedingt wird während des Beschichtungsprozesses ein Teil des Phosphors in die Schicht eingebaut, so dass eine Nickel – Legierungsschicht (Ni-P) vorliegt.
Der Phosphorgehalt der Schicht und damit auch die Schichteigenschaften lassen sich gezielt einstellen. In Abhängigkeit des Phosphorgehaltes unterscheidet man folgende Schichtsysteme:
CHEMISCH NICKEL LOW PHOS
Schichten weisen in der Regel einen Phosphorgehalt zwischen 1 – 5 % auf. Die Schichten verfügen bereits im Abscheidezustand über eine hohe Härte von etwa 750 HV 0.1 und eignen sich besonders zum Verschleißschutz temperaturempfindlicher Substrate. Typische Substratmaterialien sind deshalb Aluminium und gehärtete Stähle, da hier eine Wärmebehandlung bei Temperaturen oberhalb von 150 °C zu unerwünschten Gefügeänderungen und einem Härteabfall führen kann.
Schichten können hochglänzend abgeschieden werden. Eine Wärmebehandlung bei Temperaturen oberhalb von ca. 150 – 400 °C, führt zur Steigerung der Schichthaftung und der Schichthärte um bis zu 250 HV.
P-Gehalt | 1-5 % |
Härte Abscheidezustand | 725 – 800 HV 0.05 |
Härte nach Wärmebehandlung [350° / 2h] |
950 – 1050 HV 0.05 |
Verschleißbeständigkeit Taber Abraser CS 10 [mg / 1000 Zyklen] | |
Abscheidezustand | 6 – 10 |
Nach Wärmebehandlung [350°C / 2h] | 5 – 9 |
Zugfestigkeit [MPa] | 200 – 400 |
Bruchdehnung [%] | 0.5 – 1.5 |
E-Modul [GPa] | 55 – 65 |
Eigenspannungen auf Stahlsubstrat | leichte Druckeigenspannungen |
Schmelzpunkt [°C] | 1250 – 1350 |
Spez. elektrischer Widerstand [µΩ*cm] | 10 – 30 |
Thermischer Ausdehnungskoeffizient [µm /m / K] |
12 – 15 |
Thermische Leitfähigkeit | |
Koerzitivfeldstärke [Oe] | 15 – 80 |
Magnetische Eigenschaften der Schicht | magnetisch |
CHEMISCH NICKEL MID PHOS
Schichten weisen in der Regel einen Phosphorgehalt zwischen 5 – 10 % auf. Die Schichten verfügen im Abscheidezustand über eine hohe Härte von etwa 550 HV 0.1 und eignen sich besonders zum Einsatz bei Dispersionsschichten und Abscheidung auf allen Substraten. Typische Substratmaterialien sind Aluminium und alle Arten von Stählen und Sonderwerkstoffe.
Eine Wärmebehandlung bei Temperaturen oberhalb von ca. 150 – 400 °C, führt zur Steigerung der Schichthaftung und der Schichthärte um bis zu 250 HV.
P-Gehalt | 5-10 % |
Härte Abscheidezustand | 500 – 600 HV 0.05 |
Härte nach Wärmebehandlung [350° / 2h] |
950 – 1050 HV 0.05 |
Verschleißbeständigkeit Taber Abraser CS 10 [mg / 1000 Zyklen] | |
Abscheidezustand | 15 – 20 |
Nach Wärmebehandlung [350°C / 2h] | 10 – 12 |
Zugfestigkeit [MPa] | 800 – 1000 |
Bruchdehnung [%] | 0.5 – 1.0 |
E-Modul [GPa] | 50 – 65 |
Eigenspannungen auf Stahlsubstrat | Neutral / leichte Zugeigenspannungen |
Schmelzpunkt [°C] | 880 – 980 |
Spez. elektrischer Widerstand [µΩ*cm] | 40 – 70 |
Thermischer Ausdehnungskoeffizient [µm /m / K] |
10 – 15 |
Thermische Leitfähigkeit | |
Koerzitivfeldstärke [Oe] | 1 – 8 |
Magnetische Eigenschaften der Schicht | Schwach magnetisch |
CHEMISCH NICKEL HIGH PHOS
Schichten weisen in der Regel einen Phosphorgehalt zwischen 10 – 13 % auf. Die Schichten verfügen im Abscheidezustand über eine Härte von etwa 500 HV 0.1 , die sich durch eine Wärmebehandlung auf etwa 950 HV 0.1 steigern lässt. Diese Schichten weisen eine hervorragende Korrosionsbeständigkeit auf.
Eine Wärmebehandlung bei Temperaturen oberhalb von ca. 150 – 400 °C, führt zur Steigerung der Schichthaftung und der Schichthärte um bis zu 250 HV.
P-Gehalt | 10-13 % |
Härte Abscheidezustand | 450 – 525 HV 0.05 |
Härte nach Wärmebehandlung [350° / 2h] |
850 – 950 HV 0.05 |
Verschleißbeständigkeit Taber Abraser CS 10 [mg / 1000 Zyklen] | |
Abscheidezustand | 22 – 24 |
Nach Wärmebehandlung [350°C / 2h] | 10 – 14 |
Zugfestigkeit [MPa] | 650 – 900 |
Bruchdehnung [%] | 1.0 – 2.5 |
E-Modul [GPa] | 55 – 70 |
Eigenspannungen auf Stahlsubstrat | Neutral / leichte Druckeigenspannungen |
Schmelzpunkt [°C] | 880 – 900 |
Spez. elektrischer Widerstand [µΩ*cm] | 75 – 110 |
Thermischer Ausdehnungskoeffizient [µm /m / K] |
08 – 10 |
Thermische Leitfähigkeit | |
Koerzitivfeldstärke [Oe] | 0 |
Magnetische Eigenschaften der Schicht | unmagnetisch |
CHEMISCH NICKEL – DIAMANT MMD / PMD ist Grundlage von DIAPROTECT
Schichten werden seit Jahrzehnten erfolgreich insbesondere im Textilmaschinenbereich eingesetzt. Bevorzugt werden synthetische Diamanten mit einer mittleren Partikelgröße von 2 µm eingelagert. Die Schichten zeichnen sich durch eine hervorragende Beständigkeit gegen Abrasivverschleiß aus und bieten durch ihren heterogenen Schichtaufbau die einzigartige Möglichkeit, definierte und über die Lebensdauer der Schicht konstante Reibwerte einzustellen.
Diese Eigenschaften nutzt man insbesondere bei der Beschichtung faserführender Komponenten im Textilmaschinenbereich.
Querschliff: Chemisch Nickel – Diamant Oberflächentopographie: Chemisch Nickel – Diamant
P-Gehalt | Je nach Anforderung |
Korngröße Diamant d50 | 2 µm [4 µm; 6 µm; 10 µm] |
Einlagerungsvolumen | 25-30 % |
Schichtdicke | üblicherweise 15-50 µm |
Härte Abscheidezustand | bis 750 HV 0.01 |
Härte nach Wärmebehandlung [350° / 2h] | bis 1300 HV 0.01 |
Verschleißbeständigkeit Taber Abraser CS 10 [mg / 1000 Zyklen] | |
Abscheidezustand | 0.5 – 1.5 |
Nach Wärmebehandlung [350°C / 2h] | < 1.5 |
Einsatztemperatur | bis 500 °C |
CHEMISCH NICKEL – DIAMANT ND
Bei diesen neu entwickelten Dispersionsschichten werden Nanodiamanten in die Chemisch Nickel – Schicht eingelagert. Die Primärpartikelgröße der Diamanten beträgt nur 4-6 nm.
Focused Ion Beam: Chemisch Nickel – ND
Die Einlagerung der Nanopartikel geschieht nahezu agglomeratfrei. Obwohl die Einlagerungsrate nur 0.2 – 0.3 % beträgt, werden die Eigenschaften der Chemisch Nickel – Schichten gravierend verändert. Die Beständigkeit gegen Abrasivverschleiß wird deutlich erhöht, wie Untersuchungen mit dem Taber-Abraser – Test belegen.
Insbesondere bei Low – und Mid Phos – Schichten wird durch die Einlagerung von Nanodiamanten eine signifikante Verbesserung der Verschleißbeständigkeit selbst ohne Wärmebehandlung erreicht.
Taber Wear Index (Verschleiß in mg. nach 1000 Zyklen)
Reibrolle: CS 10
Last: 1000g
Zyklen 6*1000
Da durch die geringe Partikelgröße keine Verschleißwirkung auf den tribologischen Gegenpartner ausgeübt wird, eignen sich diese Schichten besonders für den Einsatz in geschlossenen Tribosystemen.
CHEMISCH NICKEL – DIAMANT ist Grundlage von DIAGRIP
Bei den Diagrip® Schichten von CCT nutzt man die Möglichkeit, durch die Einlagerung von Diamantpartikeln die Reibwerte einer Oberfläche gezielt zu erhöhen. Das hat besondere Vorteile bei kraftschlüssigen Verbindungen. Bei den bekannten Verbindungsarten wird zwischen formschlüssigen, stoffschlüssigen, reibschlüssigen oder Kombinationen aus den genannten Verbindungsarten unterschieden.
Die Übertragungsfähigkeit einer reibschlüssigen Verbindung ist durch die Auslegung, die Flächenpressung und dem werkstoffspezifischen Haftkoeffizienten begrenzt. Durch eine gezielte Reibungserhöhung kann jedoch eine Steigerung der Kraftübertragung ohne konstruktive Veränderungen am Bauteil erreicht werden. Ermöglicht wird dies durch den Einsatz von Diagrip® reibungserhöhenden Oberflächenschichten.
Diagrip® ist eine Chemisch-Nickel Matrix mit eingelagerten Diamanten definierter Größe und Konzentration.
Diagrip – Oberfläche in Schrägansicht und Draufsicht
Die Schichten können entweder auf dünne Folien aus Stahl oder Verbundwerkstoffen oder direkt auf ein Bauteil aufgebracht werden.
Beim Verwenden von Diagrip® – Folien oder Direktbeschichtungen werden im Vergleich zum Ausgangszustand Steigerungen der übertragbaren Kräfte bis zu 300% erreicht. Dieser Effekt b asiert auf dem Eindringen der Diamantpartikel in die Gegenflächen. Zwischen Grund- und Gegenkörper entsteht so ein Mikroformschluss, der von Material, Oberfläche und Flächenpressung der Fügepartner abhängt. Diese Modellvorstellung wird in untenstehend verdeutlicht.
Zum Einsatz kommen Diagrip® Schichten überall da, wo effiziente und sichere Kraftübertragung im Vordergrund steht. Aufgrund ihrer exzellenten Eigenschaften sind sie erste Wahl im Automobil- und Maschinenbau sowie in der Antriebstechnik. Hierzu gehören:
- Übertragung von höchsten Kräften und Drehmomenten
- Zuverlässige Erhöhung des Haftbeiwertes
- Höchstmaß an Sicherheit und Reproduzierbarkeit
- Möglichkeit von Folien oder Direktbeschichtungen gemäß Kundenspezifikation
- Problemlose Wiedermontage
- Die Wirkung von Diagrip® wird durch dünne Ölfilme oder Konservierungsmittel nicht beeinflusst
Datenblatt Diagrip – Folie
Funktionale Eigenschaften | Reibwerterhöhende Diamantbeschichtung auf Stahl- oder Composite – Folie |
Bezeichnung | DIAGRIP®10 | DIAGRIP®25 | DIAGRIP®35 |
Folienmaterial | Stahl C75 S oder GFK – Folie |
Bearbeitung | Wasserstrahlschneiden; Lasern oder Stanzen |
Farbe | Silbrig grau metallisch |
Dicke der Folie x | 0,1 mm ± 0,01 mm oder dicker |
Mittlere Partikelgröße Diamant | 10 µm | 25 µm | 35 µm |
Flächenbelegungsdichte | 10-20 % | 10-25 % | 15-30 % |
Schichtmatrix | Chemisch Nickel |
Härte Schichtmatrix | 550 – 950 HV0,1 |
Schichtdicke der Matrix y | 5-8 µm | 13-17 µm | 14-22 µm |
Magnetisch | Bei Verwendung von GFK – Folien können unmagnetische Folien hergestellt werden |
Elektrische Leitfähigkeit | Bei Verwendung von GFK – Folien können elektrisch isolierende Folien hergestellt werden |
Anforderungen | |||
Rautiefe Rz oder | Rz < 10 µm | Rz < 25 µm | Rz < 35 µm |
Mittenrauwert Ra der Gegenflächen | Rz < 1,6 µm | Rz < 3,2 µm | Rz < 6,3 µm |
Min. Flächenpressung | 50 MPa |
Max. Einsatztemperatur | 400 °C bei Stahlfolien bis 200 °C bei GFK – Folie |
CHEMISCH NICKEL SIZILIUMCARBID ist Grundlage von DIAGLIDE
Chemisch Nickel – SiC – Schichten werden zur Beschichtung von Textilmaschinen-, Druckmaschinen- und Motorenkomponenten eingesetzt.
Siliziumcarbid ist ein synthetisch hergestellter Hartstoff, der sich durch eine hohe Härte und eine im Vergleich zum Diamant eher splittrige Kornform auszeichnet.
Chemisch Nickel – SiC – Schichten zeigen hervorragende Verschleißschutzeigenschaften und eignen sich nach einer mechanischen Nachbehandlung durch Gleitschleifen oder Honen besonders als tribologischer Partner in gleitbeanspruchten Anwendungen.
Chemisch Nickel – SiC (Partikelgröße 1-4 µm)
P-Gehalt | Je nach Anforderung |
Korngröße SiC d50 | 2 µm [0,5 µm] |
Einlagerungsvolumen | 20-25 % |
Schichtdicke | üblicherweise 15-50 µm |
Härte Abscheidezustand | bis 750 HV 0.01 |
Härte nach Wärmebehandlung [350° / 2h] | bis 1150 HV 0.01 |
Verschleißbeständigkeit Taber Abraser CS 10 [mg / 1000 Zyklen] | |
Abscheidezustand | |
Nach Wärmebehandlung [350°C / 2h] | < 1.5 |
Einsatztemperatur bis 5 | 500 °C |
CHEMISCH NICKEL BORCARBID ist Grundlage von DIAPROTECT
Chemisch Nickel – B4C – Schichten werden zur Beschichtung von Textilmaschinen-, Druckmaschinen- und Motorenkomponenten eingesetzt. Borcarbid ist ein synthetisch hergestellter Hartstoff, der sich durch eine hohe Härte und besondere chemisch-physikalische Eigenschaften auszeichnet.
Chemisch Nickel – Borcarbid (Partikelgröße 2 µm)
P-Gehalt | Je nach Anforderung |
Korngröße SiC d50 | 2 µm [0,5 µm] |
Einlagerungsvolumen | 20-25 % |
Schichtdicke | üblicherweise 15-50 µm |
Härte Abscheidezustand | bis 750 HV 0.01 |
Härte nach Wärmebehandlung [350° / 2h] | bis 1150 HV 0.01 |
Verschleißbeständigkeit Taber Abraser CS 10 [mg / 1000 Zyklen] | |
Abscheidezustand | |
Nach Wärmebehandlung [350°C / 2h] | < 1.5 |
Einsatztemperatur bis 5 | 500 °C |
CHEMISCH NICKEL – DISPERSIONSSCHICHTEN MIT EINGELAGERTEN FESTSCHMIERSTOFFEN sind Grundlage von DIASHIELD
Diese Schichtsysteme finden bevorzugt Anwendung, wenn in gleitbeanspruchten tribologischen Systemen Adhäsivverschleiß verhindert werden soll. Die Schmierwirkung der eingelagerten Festschmierstoffe beruht darauf, dass sie während des Gleitvorganges die beiden Kontaktflächen durch Bildung von Zwischenschichten trennen und / oder diese so verändern, dass kein direkter Metall / Metall-Kontakt und damit kein Verschleiß stattfinden kann.
Die Schmierwirksamkeit von PTFE beruht auf der Entstehung einer adhäsiven Bindung im Reibkontakt. PTFE – Moleküle werden geschert und es entsteht ein Transferfilm in der Kontaktzone.
CHEMISCH NICKEL – PTFE / HBN
Chemisch Nickel – PTFE – Schichten zeigen durch die geringe Härte der eingelagerten Partikel eine vergleichsweise geringe Beständigkeit gegen Abrasivverschleiß . Die thermische Aushärtung der Schichten ist durch die Temperaturempfindlichkeit der PTFE-Partikel auf etwa 290 °C begrenzt. Diese Temperaturgrenze limitiert natürlich auch das thermische Einsatzspektrum solcher Schichtsysteme erheblich.
Bei geeigneten Einsatzbedingungen zeigen die Chemisch Nickel – PTFE – Schichten einen sehr niedrigen Reibwert auch im ungeschmierten Zustand sowie eine deutliche Reduzierung des Stick-Slip – Effektes. Ebenfalls erwähnenswert sind die ausgeprägten antiadhäsiven Eigenschaften der Schicht, die technisch vielfältig genutzt werden können.
Querschliff Chem. Nickel – PTFE (Partikelgröße 0.5 µm)
P-Gehalt | Je nach Anforderung |
Korngröße PTFE d50 | 0,5 µm |
Einlagerungsvolumen | 20-25 % |
Schichtdicke | üblicherweise 5-20 µm |
Härte Abscheidezustand | bis 350 HV 0.01 |
Härte nach Wärmebehandlung [350° / 2h] | bis 500 HV 0.01 |
Verschleißbeständigkeit Taber Abraser CS 10 [mg / 1000 Zyklen] | |
Abscheidezustand | |
Nach Wärmebehandlung [350°C / 2h] | |
Einsatztemperatur bis | 270 °C |
Chemisch Nickel
Daraus resultieren die besonderen Eigenschaften dieser Schichten:
Die chemische Metallabscheidung gewährleistet eine sehr konstante und gleichmäßige Schichtdickenverteilung auch bei Bauteilen komplexer Geometrie.
Auch Innengeometrien, Bohrungen und Hinterschneidungen werden absolut gleichmäßig beschichtet.
Zur Abscheidung der Chemisch Nickel – Schichten wird ein Reduktionsmittel benötigt. In den meisten Fällen handelt es sich dabei um eine phosphorhaltige Verbindung. Verfahrensbedingt wird während des Beschichtungsprozesses ein Teil des Phosphors in die Schicht eingebaut, so dass eine Nickel – Legierungsschicht (Ni-P) vorliegt.
Der Phosphorgehalt der Schicht und damit auch die Schichteigenschaften lassen sich gezielt einstellen. In Abhängigkeit des Phosphorgehaltes unterscheidet man folgende Schichtsysteme:
CHEMISCH NICKEL LOW PHOS
Schichten weisen in der Regel einen Phosphorgehalt zwischen 1 – 5 % auf. Die Schichten verfügen bereits im Abscheidezustand über eine hohe Härte von etwa 750 HV 0.1 und eignen sich besonders zum Verschleißschutz temperaturempfindlicher Substrate. Typische Substratmaterialien sind deshalb Aluminium und gehärtete Stähle, da hier eine Wärmebehandlung bei Temperaturen oberhalb von 150 °C zu unerwünschten Gefügeänderungen und einem Härteabfall führen kann.
Schichten können hochglänzend abgeschieden werden. Eine Wärmebehandlung bei Temperaturen oberhalb von ca. 150 – 400 °C, führt zur Steigerung der Schichthaftung und der Schichthärte um bis zu 250 HV.
P-Gehalt | 1-5 % |
Härte Abscheidezustand | 725 – 800 HV 0.05 |
Härte nach Wärmebehandlung [350° / 2h] |
950 – 1050 HV 0.05 |
Verschleißbeständigkeit Taber Abraser CS 10 [mg / 1000 Zyklen] | |
Abscheidezustand | 6 – 10 |
Nach Wärmebehandlung [350°C / 2h] | 5 – 9 |
Zugfestigkeit [MPa] | 200 – 400 |
Bruchdehnung [%] | 0.5 – 1.5 |
E-Modul [GPa] | 55 – 65 |
Eigenspannungen auf Stahlsubstrat | leichte Druckeigenspannungen |
Schmelzpunkt [°C] | 1250 – 1350 |
Spez. elektrischer Widerstand [µΩ*cm] | 10 – 30 |
Thermischer Ausdehnungskoeffizient [µm /m / K] |
12 – 15 |
Thermische Leitfähigkeit | |
Koerzitivfeldstärke [Oe] | 15 – 80 |
Magnetische Eigenschaften der Schicht | magnetisch |
CHEMISCH NICKEL MID PHOS
Schichten weisen in der Regel einen Phosphorgehalt zwischen 5 – 10 % auf. Die Schichten verfügen im Abscheidezustand über eine hohe Härte von etwa 550 HV 0.1 und eignen sich besonders zum Einsatz bei Dispersionsschichten und Abscheidung auf allen Substraten. Typische Substratmaterialien sind Aluminium und alle Arten von Stählen und Sonderwerkstoffe.
Eine Wärmebehandlung bei Temperaturen oberhalb von ca. 150 – 400 °C, führt zur Steigerung der Schichthaftung und der Schichthärte um bis zu 250 HV.
P-Gehalt | 5-10 % |
Härte Abscheidezustand | 500 – 600 HV 0.05 |
Härte nach Wärmebehandlung [350° / 2h] |
950 – 1050 HV 0.05 |
Verschleißbeständigkeit Taber Abraser CS 10 [mg / 1000 Zyklen] | |
Abscheidezustand | 15 – 20 |
Nach Wärmebehandlung [350°C / 2h] | 10 – 12 |
Zugfestigkeit [MPa] | 800 – 1000 |
Bruchdehnung [%] | 0.5 – 1.0 |
E-Modul [GPa] | 50 – 65 |
Eigenspannungen auf Stahlsubstrat | Neutral / leichte Zugeigenspannungen |
Schmelzpunkt [°C] | 880 – 980 |
Spez. elektrischer Widerstand [µΩ*cm] | 40 – 70 |
Thermischer Ausdehnungskoeffizient [µm /m / K] |
10 – 15 |
Thermische Leitfähigkeit | |
Koerzitivfeldstärke [Oe] | 1 – 8 |
Magnetische Eigenschaften der Schicht | Schwach magnetisch |
CHEMISCH NICKEL HIGH PHOS
Schichten weisen in der Regel einen Phosphorgehalt zwischen 10 – 13 % auf. Die Schichten verfügen im Abscheidezustand über eine Härte von etwa 500 HV 0.1 , die sich durch eine Wärmebehandlung auf etwa 950 HV 0.1 steigern lässt. Diese Schichten weisen eine hervorragende Korrosionsbeständigkeit auf.
Eine Wärmebehandlung bei Temperaturen oberhalb von ca. 150 – 400 °C, führt zur Steigerung der Schichthaftung und der Schichthärte um bis zu 250 HV.
P-Gehalt | 10-13 % |
Härte Abscheidezustand | 450 – 525 HV 0.05 |
Härte nach Wärmebehandlung [350° / 2h] |
850 – 950 HV 0.05 |
Verschleißbeständigkeit Taber Abraser CS 10 [mg / 1000 Zyklen] | |
Abscheidezustand | 22 – 24 |
Nach Wärmebehandlung [350°C / 2h] | 10 – 14 |
Zugfestigkeit [MPa] | 650 – 900 |
Bruchdehnung [%] | 1.0 – 2.5 |
E-Modul [GPa] | 55 – 70 |
Eigenspannungen auf Stahlsubstrat | Neutral / leichte Druckeigenspannungen |
Schmelzpunkt [°C] | 880 – 900 |
Spez. elektrischer Widerstand [µΩ*cm] | 75 – 110 |
Thermischer Ausdehnungskoeffizient [µm /m / K] |
08 – 10 |
Thermische Leitfähigkeit | |
Koerzitivfeldstärke [Oe] | 0 |
Magnetische Eigenschaften der Schicht | unmagnetisch |
Chem. Nickel Dispersion
CHEMISCH NICKEL – DIAMANT MMD / PMD
Schichten werden seit Jahrzehnten erfolgreich insbesondere im Textilmaschinenbereich eingesetzt. Bevorzugt werden synthetische Diamanten mit einer mittleren Partikelgröße von 2 µm eingelagert. Die Schichten zeichnen sich durch eine hervorragende Beständigkeit gegen Abrasivverschleiß aus und bieten durch ihren heterogenen Schichtaufbau die einzigartige Möglichkeit, definierte und über die Lebensdauer der Schicht konstante Reibwerte einzustellen.
Diese Eigenschaften nutzt man insbesondere bei der Beschichtung faserführender Komponenten im Textilmaschinenbereich.
Querschliff: Chemisch Nickel – Diamant Oberflächentopographie: Chemisch Nickel – Diamant
P-Gehalt | Je nach Anforderung |
Korngröße Diamant d50 | 2 µm [4 µm; 6 µm; 10 µm] |
Einlagerungsvolumen | 25-30 % |
Schichtdicke | üblicherweise 15-50 µm |
Härte Abscheidezustand | bis 750 HV 0.01 |
Härte nach Wärmebehandlung [350° / 2h] | bis 1300 HV 0.01 |
Verschleißbeständigkeit Taber Abraser CS 10 [mg / 1000 Zyklen] | |
Abscheidezustand | 0.5 – 1.5 |
Nach Wärmebehandlung [350°C / 2h] | < 1.5 |
Einsatztemperatur | bis 500 °C |
CHEMISCH NICKEL – DIAMANT ND
Bei diesen neu entwickelten Dispersionsschichten werden Nanodiamanten in die Chemisch Nickel – Schicht eingelagert. Die Primärpartikelgröße der Diamanten beträgt nur 4-6 nm.
Focused Ion Beam: Chemisch Nickel – ND
Die Einlagerung der Nanopartikel geschieht nahezu agglomeratfrei. Obwohl die Einlagerungsrate nur 0.2 – 0.3 % beträgt, werden die Eigenschaften der Chemisch Nickel – Schichten gravierend verändert. Die Beständigkeit gegen Abrasivverschleiß wird deutlich erhöht, wie Untersuchungen mit dem Taber-Abraser – Test belegen.
Insbesondere bei Low – und Mid Phos – Schichten wird durch die Einlagerung von Nanodiamanten eine signifikante Verbesserung der Verschleißbeständigkeit selbst ohne Wärmebehandlung erreicht.
Taber Wear Index (Verschleiß in mg. nach 1000 Zyklen)
Reibrolle: CS 10
Last: 1000g
Zyklen 6*1000
Da durch die geringe Partikelgröße keine Verschleißwirkung auf den tribologischen Gegenpartner ausgeübt wird, eignen sich diese Schichten besonders für den Einsatz in geschlossenen Tribosystemen.
Chem. Nickel Diagrip
CHEMISCH NICKEL – DIAMANT DIAGRIP
Bei den Diagrip® Schichten von CCT nutzt man die Möglichkeit, durch die Einlagerung von Diamantpartikeln die Reibwerte einer Oberfläche gezielt zu erhöhen. Das hat besondere Vorteile bei kraftschlüssigen Verbindungen. Bei den bekannten Verbindungsarten wird zwischen formschlüssigen, stoffschlüssigen, reibschlüssigen oder Kombinationen aus den genannten Verbindungsarten unterschieden.
Die Übertragungsfähigkeit einer reibschlüssigen Verbindung ist durch die Auslegung, die Flächenpressung und dem werkstoffspezifischen Haftkoeffizienten begrenzt. Durch eine gezielte Reibungserhöhung kann jedoch eine Steigerung der Kraftübertragung ohne konstruktive Veränderungen am Bauteil erreicht werden. Ermöglicht wird dies durch den Einsatz von Diagrip® reibungserhöhenden Oberflächenschichten.
Diagrip® ist eine Chemisch-Nickel Matrix mit eingelagerten Diamanten definierter Größe und Konzentration.
Diagrip – Oberfläche in Schrägansicht und Draufsicht
Die Schichten können entweder auf dünne Folien aus Stahl oder Verbundwerkstoffen oder direkt auf ein Bauteil aufgebracht werden.
Beim Verwenden von Diagrip® – Folien oder Direktbeschichtungen werden im Vergleich zum Ausgangszustand Steigerungen der übertragbaren Kräfte bis zu 300% erreicht. Dieser Effekt b asiert auf dem Eindringen der Diamantpartikel in die Gegenflächen. Zwischen Grund- und Gegenkörper entsteht so ein Mikroformschluss, der von Material, Oberfläche und Flächenpressung der Fügepartner abhängt. Diese Modellvorstellung wird in untenstehend verdeutlicht.
Zum Einsatz kommen Diagrip® Schichten überall da, wo effiziente und sichere Kraftübertragung im Vordergrund steht. Aufgrund ihrer exzellenten Eigenschaften sind sie erste Wahl im Automobil- und Maschinenbau sowie in der Antriebstechnik. Hierzu gehören:
- Übertragung von höchsten Kräften und Drehmomenten
- Zuverlässige Erhöhung des Haftbeiwertes
- Höchstmaß an Sicherheit und Reproduzierbarkeit
- Möglichkeit von Folien oder Direktbeschichtungen gemäß Kundenspezifikation
- Problemlose Wiedermontage
- Die Wirkung von Diagrip® wird durch dünne Ölfilme oder Konservierungsmittel nicht beeinflusst
Datenblatt Diagrip – Folie
Funktionale Eigenschaften | Reibwerterhöhende Diamantbeschichtung auf Stahl- oder Composite – Folie |
Bezeichnung | DIAGRIP®10 | DIAGRIP®25 | DIAGRIP®35 |
Folienmaterial | Stahl C75 S oder GFK – Folie |
Bearbeitung | Wasserstrahlschneiden; Lasern oder Stanzen |
Farbe | Silbrig grau metallisch |
Dicke der Folie x | 0,1 mm ± 0,01 mm oder dicker |
Mittlere Partikelgröße Diamant | 10 µm | 25 µm | 35 µm |
Flächenbelegungsdichte | 10-20 % | 10-25 % | 15-30 % |
Schichtmatrix | Chemisch Nickel |
Härte Schichtmatrix | 550 – 950 HV0,1 |
Schichtdicke der Matrix y | 5-8 µm | 13-17 µm | 14-22 µm |
Magnetisch | Bei Verwendung von GFK – Folien können unmagnetische Folien hergestellt werden |
Elektrische Leitfähigkeit | Bei Verwendung von GFK – Folien können elektrisch isolierende Folien hergestellt werden |
Anforderungen | |||
Rautiefe Rz oder | Rz < 10 µm | Rz < 25 µm | Rz < 35 µm |
Mittenrauwert Ra der Gegenflächen | Rz < 1,6 µm | Rz < 3,2 µm | Rz < 6,3 µm |
Min. Flächenpressung | 50 MPa |
Max. Einsatztemperatur | 400 °C bei Stahlfolien bis 200 °C bei GFK – Folie |
Chem. Nickel Siliziumcarbid
CHEMISCH NICKEL SIZILIUMCARBID
Chemisch Nickel – SiC – Schichten werden zur Beschichtung von Textilmaschinen-, Druckmaschinen- und Motorenkomponenten eingesetzt.
Siliziumcarbid ist ein synthetisch hergestellter Hartstoff, der sich durch eine hohe Härte und eine im Vergleich zum Diamant eher splittrige Kornform auszeichnet.
Chemisch Nickel – SiC – Schichten zeigen hervorragende Verschleißschutzeigenschaften und eignen sich nach einer mechanischen Nachbehandlung durch Gleitschleifen oder Honen besonders als tribologischer Partner in gleitbeanspruchten Anwendungen.
Chemisch Nickel – SiC (Partikelgröße 1-4 µm)
P-Gehalt | Je nach Anforderung |
Korngröße SiC d50 | 2 µm [0,5 µm] |
Einlagerungsvolumen | 20-25 % |
Schichtdicke | üblicherweise 15-50 µm |
Härte Abscheidezustand | bis 750 HV 0.01 |
Härte nach Wärmebehandlung [350° / 2h] | bis 1150 HV 0.01 |
Verschleißbeständigkeit Taber Abraser CS 10 [mg / 1000 Zyklen] | |
Abscheidezustand | |
Nach Wärmebehandlung [350°C / 2h] | < 1.5 |
Einsatztemperatur bis 5 | 500 °C |
Chem. Nickel Borcarbid
CHEMISCH NICKEL BORCARBID
Chemisch Nickel – B4C – Schichten werden zur Beschichtung von Textilmaschinen-, Druckmaschinen- und Motorenkomponenten eingesetzt. Borcarbid ist ein synthetisch hergestellter Hartstoff, der sich durch eine hohe Härte und besondere chemisch-physikalische Eigenschaften auszeichnet.
Chemisch Nickel – Borcarbid (Partikelgröße 2 µm)
P-Gehalt | Je nach Anforderung |
Korngröße SiC d50 | 2 µm [0,5 µm] |
Einlagerungsvolumen | 20-25 % |
Schichtdicke | üblicherweise 15-50 µm |
Härte Abscheidezustand | bis 750 HV 0.01 |
Härte nach Wärmebehandlung [350° / 2h] | bis 1150 HV 0.01 |
Verschleißbeständigkeit Taber Abraser CS 10 [mg / 1000 Zyklen] | |
Abscheidezustand | |
Nach Wärmebehandlung [350°C / 2h] | < 1.5 |
Einsatztemperatur bis 5 | 500 °C |
Chem. Nickel PTFE/HBN
CHEMISCH NICKEL – DISPERSIONSSCHICHTEN MIT EINGELAGERTEN FESTSCHMIERSTOFFEN
Diese Schichtsysteme finden bevorzugt Anwendung, wenn in gleitbeanspruchten tribologischen Systemen Adhäsivverschleiß verhindert werden soll. Die Schmierwirkung der eingelagerten Festschmierstoffe beruht darauf, dass sie während des Gleitvorganges die beiden Kontaktflächen durch Bildung von Zwischenschichten trennen und / oder diese so verändern, dass kein direkter Metall / Metall-Kontakt und damit kein Verschleiß stattfinden kann.
Die Schmierwirksamkeit von PTFE beruht auf der Entstehung einer adhäsiven Bindung im Reibkontakt. PTFE – Moleküle werden geschert und es entsteht ein Transferfilm in der Kontaktzone.
CHEMISCH NICKEL – PTFE / HBN
Chemisch Nickel – PTFE – Schichten zeigen durch die geringe Härte der eingelagerten Partikel eine vergleichsweise geringe Beständigkeit gegen Abrasivverschleiß . Die thermische Aushärtung der Schichten ist durch die Temperaturempfindlichkeit der PTFE-Partikel auf etwa 290 °C begrenzt. Diese Temperaturgrenze limitiert natürlich auch das thermische Einsatzspektrum solcher Schichtsysteme erheblich.
Bei geeigneten Einsatzbedingungen zeigen die Chemisch Nickel – PTFE – Schichten einen sehr niedrigen Reibwert auch im ungeschmierten Zustand sowie eine deutliche Reduzierung des Stick-Slip – Effektes. Ebenfalls erwähnenswert sind die ausgeprägten antiadhäsiven Eigenschaften der Schicht, die technisch vielfältig genutzt werden können.
Querschliff Chem. Nickel – PTFE (Partikelgröße 0.5 µm)
P-Gehalt | Je nach Anforderung |
Korngröße PTFE d50 | 0,5 µm |
Einlagerungsvolumen | 20-25 % |
Schichtdicke | üblicherweise 5-20 µm |
Härte Abscheidezustand | bis 350 HV 0.01 |
Härte nach Wärmebehandlung [350° / 2h] | bis 500 HV 0.01 |
Verschleißbeständigkeit Taber Abraser CS 10 [mg / 1000 Zyklen] | |
Abscheidezustand | |
Nach Wärmebehandlung [350°C / 2h] | |
Einsatztemperatur bis | 270 °C |
Kontakt